Barrington Cement Works - Cambridgeshire
2017 to 2020
Probably, I can't remember.
2017 to 2020
Probably, I can't remember.
Sources and Further reading:
News of Closure:
BBC News
Primary Source:
Cement Kilns UK: Barrington
General History and Mechanicals:
Graces Guide: 1931 Publication
Graces Guide: Eastwood Group (1934 Review)
Jonathan Spains Blog: Chivers Fruit and Eastwoods Dispute
Money Week: Farrows Bank Fraud
Wonders Of Engineering: Cement
The Railway
Great Eastern Traction: Locomotives
Rocks By Rail: Tippler Wagons
An Introduction
This report is now rather old and like the Houghton Grange report relies on numerous old and poorly taken photos, by a much younger and naïve self. Unlike the other report, mentioned merely but a sentence ago, I haven't had the chance to go back and re-document missed areas so for that we will just have to imagine what they looked like.
If I remember correctly the first visit here was around Mid to Late 2017 although it may have been earlier. The first knowledge of the place came from a lead on this forum posted after the site went from being mothballed to decommissioned.
Initial source:
Report - - Cemex, Barrington Works, December 2012 | Industrial Sites
Visited with Bordello and Fredster Peterson. This was posted up as a rumour some time last year but since then I've not heard a word about it. Seeing as I was in the south over the holidays I thought it'd be rude not to have a pop. Cemex were the owners of the Barrington Cement Works site until...
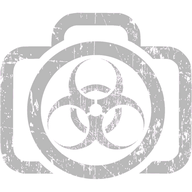
A Run Down.
Visited with: Xplorer.x for the most part.
At the time most of our weekends were spent in clapped out warehouses or other regrettable places making this almost the holy-grail for us at the time.
Having an interest, even then, of large scale machinery seeing even some of this from above by satellite imagery was beyond exciting. Then knowing that the centre piece being the slightly cut in half FLSmidth rotary kiln, was essentially a rusting hulk of mass pryo-processing equipment, it began to cement my interest with this place as a whole. It was then that Barrington started to form itself as probably one of the core memories in this hobby.
Over the uncountable visits here, although we didn't find anything new each time, a lot of the time spent here was rather enjoyable which helped captivate the "exploring" element of this hobby. Adding to the fact, there wasn't any security to speak of towards the start, we near enough had free reign of the place upon each visit which helped relax any anxieties and allowed us to focus on wandering around.
Barrington (Operational From 1927 - 2008 (with some use into 2009.))
Barrington, a small Cambridgeshire village, became home to one of the many quarries used for cement making in what was becoming known as the Cam Valley.
The Cam Valley (in short) is one of three prominent regions on which the bands of chalk provide excellent cement making material. The chalk spreads from the Chilterns towards North-East Anglia (along predominantly the river Cam, in which Cambridge is named after.), The Thames and towards Kent.
Specifically the chalk along the Cam Valley is greater exposed down to that of the Lower Chalk Marl layer which can be dated to around 100 Million Years. The Chalk Marl yields a higher percentage, upwards of 70%, of calcium within which popularised the material as a Natural Cement, easy to process, bringing an uprising of cement works in the late 1800's when Portland Cement became more popular.
It was sooner revealed that the originally implemented methods of manufacture for this claimed natural cement had been inadequate and it lead to few of the Cam Valley plants surviving past the mid 20th century with Barrington and Norman being the two outliers.
This region and some of the surrounding areas also allowed for brick making with differing grades of clay and chalk allowing for the establishment of industries such as Stewartby in the production of fletton brick.
Portland Cement, it should be mentioned, is the most common type of cement used today in the making of materials such as mortar and concrete. The material's creation can be traced back to around the mid 1800's under Joseph Aspdin, a Leeds born bricklayer, who patented the product name in 1824 with the name's routes being traced to Dorset's Portland stone.
Portland cement is known as a hydraulic cement which hardens using water and then becomes resistant to water once hardened.
The basic make up of the material usually consists of a Limestone and a Clay, with the addition of a aluminium containing material, which at the time of Joseph's patent in 1824 was intended to replicate that of Portland Stone used for structures such as St Pauls Cathedral. It was created by grinding the materials of Clay (High in Silicate) and Limestone (High in Calcium) together then heating this mix to approximately 1400oC where they begin to sinter together and form a clinker. The clinker is then crushed along with a calcium sulphate containing material (Gypsum) to help create the final product once mixed with water: Portland cement.
Wikipedia: Portland Cement
The modern technique which creates Portland cement, in a heavily simplified manner, consists of three main stages after quarrying.
- Mixing of a High Calcuim and Low Calcium raw material, in a Raw Mill.
- Pyro-processing stage which calcinates the materials into clinker, usually using a Kiln.
- Clinker crushed to a power with any final materials added or processes applied, Usually within a Ball Mill.
All of which are things that can be seen within a cement works such as Barrington.
Cement Kilns UK: Cement Plant Layout
Back to Barrington
-1914
The Dreadnought Portland Cement Company
The beginnings of Barrington are entailed with fraud and numerous issues which near enough shut down the potential for cement making at Barrington years before manufacture could finally begin.
The Dreadnought Portland Cement Company would be the hopeful first operator of the plant, directed by Walter Forder and initially funded by Farrow's Bank, having purchased the 151acre Hill Farm which stretched from the High Road to Barrington Hill. The purchase came in at a cost of £6,000, eating into the initial £20,000 of the prospected £50,000 loaned to the company, with the land surveys promising clay deposits suitable for the production of Portland Cement.
Horace Boot and Partners were contracted as the consulting engineers (Walter and Horace being former colleagues) for construction of Barrington with the first items constructed primarily were that of the Powerhouse and its' chimney by 1915. Although at the beginnings of the World War construction halted.
It is unknown at this point what supplier had been selected as the manufacturer of the kilns and cement making equipment as there hadn't been much planned for it, but judging by work at a related plant it was likely to have been Polysius or Vickers.
In the beginning of 1917 efforts began once again to continue progress on the plant although one of the more pressing issues was to establish a transport connection out of the works for materials. With Foxton in close proximity the railway was selected as this allowed access to London through Hitchin and access north through Ely although a spur was required to be constructed from the station to the works. The major hurdle was the unwillingness of the landowners to sell up and a compulsory purchase agreement was applied for through an inquiry but ultimately denied (Jan 1917). A second attempt in 1919 would be successful with the probable threat of importing German cement a concern played upon by the Dreadnought company to push forward construction. Highlighted in the inquiries was the money already pushed into the works having now apparently exceeded £20,000 and later £23,000 in 1919.
A year later a series falsified balance sheets, created by the re-valuing of investments, was uncovered by investors of the Dreadnought Company's investors. The falsification of the books made it seem as if the bank was actually turning a profit when in reality it was haemorrhaging money. Farrows Bank had initially invested £50,000 into Barrington which later showed the bank had now given the Dreadnought Company a value of over £750,000 and this soon saw the demise of the Dreadnought company in 1921 also seeing Thomas Farrow convicted of fraud.
The assets and land were put up to sale including living quarters for managerial staff, the power house, smaller buildings and the railway line.
Dreadnought did not disappear as a company entirely but was instead re-established as an investment trust by the following operators for construction of another plant.
Buyers for the land didn't step up as quickly as anticipated, seeing that the works required to begin cement making involved basically building it from the ground up, with only a few minor structures being already in place. Eventually in 1924 Eastwoods Cement would take up the purchase of the assets and land for £6,000.
-1924
Eastwoods Cement Limited
Eastwoods was a company that had routes traceable back to the early 1800's with the creation spurred by a desperate need for construction materials appearing in Kent and by the late 1800's was selling Lime, Portland Cement and Bricks. By the time they took up the land of Barrington the company had reorganised into Eastwoods and Co in 1920, with Eastwoods Cement Ltd appearing in 1925, specialising as brick makers and established builder's merchants as well as holding ownership several wharfs and barges.
As mentioned merely a sentence ago, Eastwoods would split into Eastwoods Cement Ltd in 1925 with Barrington being their first plunge into cement making on such a scale followed by their takeover of Lewes Cement in 1929 and later construction of South Ferriby in 1938. Within this they would spur the creation of the Barrington Railway Company. With the creation of this new company Horace Boot, the former Consulting Engineer under Dreadnought, would find himself as the managing director.
After the purchase in 1924 and the creation of Eastwoods Cement in 1925, construction of the required assets began to take place. Most of the cement making equipment was under the delivery of the Sheffield based Vickers. Although new to construction of cement making equipment Vickers had an already proven record, and by the time of completion would eventually merge with Vickers Whitworth to form Vickers Armstrong.
Production would start around July 1927, in just shy of two years from construction, with a Vickers Armstrong kiln at the centre fuelled by coal and capable of allowing the works to produce well over 180 Ton per day (or approximately the mass of 170 NB Mazda MX5s). Similar in design to Shoreham the coolers were under the kiln with the Slurry fed into the kiln as a wet mixture.
The raw chalk, also known as "Clunch", would be quarried on site with a steam excavator before loaded onto a series of wagons. The wagons, hauled on Barrington's internal light railway, would arrive into one of three wash-mills where it is processed.
The whole works had an internal power station with three Babcock and Wilcox boilers creating an output of 550V at 50Hertz produced from two Turbines and a reserve steam Engine.
Shortly after production beginning construction of a secondary kiln, identical to No1, would be completed in 1931 to increase capacity and meet demands. This lead to 2,800 Ton of material capable of being produced per week.
In addition to increased clinker production the power plant on site was already outdated, having been built by the start of WW1, and to increase output waste heat boilers were implemented onto the pair of kilns. Although, even once implemented, inefficiency would be an issue that would plague Barrington for years to come. The Kilns themselves consumed around 10 Mega Joules of energy for every Kilo processed and although improved to around 8MJ post WW2 these were still comparatively inefficient.
Operations continued at a steady pace onwards with almost all remaining cam valley plants having now closed by the mid 30's with Barrington and Norman being the remainders. Barrington would remain relatively unchanged during the war period.
1956 would see Barrington welcome a third Vickers Armstrong wet-process cement kiln onto the site again boosting output of the works. By this time most plants were beginning to venture into more efficient dry or semi-dry process kilns, supplied from FLS or Polysius, which would further exaggerate Barrington's efficiency issues by using older and more simplified equipment.
-1962
Rugby Portland Cement Company / Rugby Group.
Eastwoods had now formed all of its subsidiaries into one firm and in 1962/3 would be sold to Rugby (and then sold to Redland holdings and then back to rugby) which would see their cement plant operations taken into their control under Rugby Portland Cement. Soon after Rugby would commission Barrington's first Non-Vickers built rotary kiln and instead opt for the Danish firm of FLSmidth & Co. to deliver kiln A4.
Coming into service in 1964 kiln A4 would still run as a wet process, slurry fed, kiln in the same regard to A1-A3 and would use newer equipment for the coal mills. Unlike the original trio, A4 would instead opt for a FLS Unax variant of a planetary cooler design and boast a far more efficient heat consumption of over 7MJ per KG. It would share similarities to more modern cement plants at this point, presumably making Barrington more competitive, although the inherent design of the plant would still hinder the operations. (Cement Kilns: Planetary Coolers)
At the same time the initial kiln exhaust systems would be revised to reduce dust with the original cyclone fans replaced with electrostatic precipitators to dampen the dust exhausted from the stacks meeting the standards of the newer kilns' system.
The three Raw mills, which washed and prepared the material for pyro-processing, would also see an overhaul with the initial three replaced for pair of higher powered 560kw mills. At this point all the main points of operation would still be interlinked by the railway system.
Despite the aging infrastructure of the works Rugby still found Barrington as one of their lowest cost to operate. The primary cause of this was presumably the simplicity of the equipment.
Rugby as a whole would soon see production of over 2.5Million ton of cement each year by the 1970s with Barrington's kilns capable of contributing around 1,400 tons on a daily basis.
Continuing on until the 90's Rugby would soon shut down kilns A1 to A3 with their associated equipment and demolishing what remained shortly after. Presumably due to the age of the equipment as well as changing demands within the industry. A few years prior Rugby had also updated A4s fuel feed to now mostly rely on Petroleum Coke with the addition of liquid waste (such as oil) as a means of lowering cost.
-2000
RMC
In 2000 rugby cement would be taken over by the Ready Mix Concrete Group, founded 1930, who were growing their interests into cement manufacture at the time. Most of the operational Rugby plants would remain open although Rochester and Southam would see closure almost instantly after the takeover.
-2005
Cemex
Operations under RMC would only last a few years until 2005 in which they would be sold to Cemex enlarging the operational capacity of Cemex outside of Mexico. As the new operator began to oversee operations updates would be implemented into all of their plants with Barrington and related plants all seeing their kiln fuels switched over to solid waste, which would otherwise end as landfill, further lowering the cost of powering the plants.
Barrington in specific would see one of its' identifying features, the internal railway, closed in favour of more commonly used tipper trucks with the locomotives and wagons mothballed and later sold or donated. Cemex would apply for permission to construct a replacement washmill and rawmill at the same point in time.
Continuing, Cemex would venture into cutting operational costs across their UK operations with the plan to use the extra capacity within their two former Rugby plants allowing Barrington to finally shutdown. This was also attributed to a decline in the construction industry as well as the inherent age of Barrington but they planned for Barrington to to remain partially open until 2009 even after the closure of the kiln in 2008.
Post closure the kiln would see partial demolition around 2012 before being left again. Cemex would open up the pit for landfill operations utilising the railway link to dump dirt and other wastes from major engineering projects such as Crossrail. Eventually in the beginnings of 2018 Redrow homes would start developments on the works alongside Erith demolition.
Today very little remains, the wash mill is partially intact although under a watchful eye and due for demolition, the areas where the clinker store and kiln stood now garner a set of houses with the rest soon to see the same treatment.
The Map
Constructed using older maps, prior to full demolition, here is a rough layout of the plant at the time of closure overlaid onto a current view. (Minor structures omitted)
The primary structures covered involve the Kiln, Cement Mill and Washmill with a few of the ancillary structures.
The internal railway is roughly marked but I cannot confirm the accuracy of my illustration.
In no specific order
A: Washmill
B: Kiln Chimney and a Slurry Tank
C: Kiln House (Control Room and Related Kiln Equipment)
D: Railway Unloading/Maint Shed (No Coverage)
E: Clinker Store and Cement Mill
F: Offices, Labs and Mess (No Coverage)
G: Silos and Bagging Plant (Partially Covered)
H: Vehicle Shed (Partial Coverage)
The Visits
The first time I stepped foot on site would have been at some point in the closing months of 2017. At the time most of our knowledge in the hobby was based among childish anxieties that you'd first suspect when brand new into this silly hobby which lead to us choosing the most isolated part of the works to start in.
After a bit of scrambling around in circles we would finally get inside and whipped out our state of the art photography equipment consisting of an iPhone and a Poundland torch before being spooked by something and departing. On the way out it only took a few sightings on the larger buildings to realise we needed to dive further in.
We'd revisit a few more times in the remainder of the year before around may 2018 where I'd take a look back at the works with a sibling. We decided to discard any worries and make our way directly to the main building of our interests, the Kiln, to see what would be on offer. Climbing along the gas and water pipes that were loosely attached to the building's frame we walked into a small back area where we would finally find the control room which instantly took my interest.
From that point onwards numerous return visits would be on the cards knowing that there was more to this works than a few old items lying about. As security upped to a series of frantic patrols and sitting vans the enjoyment of poking around the works grew and we started treating it as a game, thankfully without any capture. We began to tick off the list as we went along The Kiln, Control Room, The Ball Mill, The bagging plant, The washmill, and numerous smaller buildings until we felt that we had seen it all.
Later into 2018 the demolition teams would turn up and it soon became apparent that our fun was over. We used this as an excuse to finalise anything we had yet to have covered before calling it a day at Barrington.
Anyway, probably time to crack on with the limited photos.
A: Washmill and slurry mixers
This section was comprised of several structures with two being of the most interest although the process used helps understand what is going on.
Using the railway system wagons would first arrive at the waggon tippler where they would be uncoupled and tipped into pits which would take the raw clay and chalk up to the first part of the process. The tipplers had long since been demolished and the conveyors only remained.
After being conveyed into the plant the materials would b dumped into large mixing pools for separating the minerals. Above this are the motors and power equipment.
The building immediately next door.
The secondary building.
B: The Kiln Chimney and Surry Tank.
These two structures have no direct connection within their operations but with their proximity being rather close these will compiled as a pair.
The chimney was cut from the kiln when it was partly scrapped around 2012 which then only remained as the stack and precipitators.
The slurry tank didn't seem to make much sense in its' location, to myself, but the electrical backrooms would provide some interest.
G: Storage Silos
These were the most prominent of the structures on site when driving or walking past, yet always proved to be a slight struggle to gain access to.
H: The Vehicle Shed
The least impressive structure this was reflective of your usual disused warehouse.
C: The Kiln House
This was the heart of the plant, to be philosophical, and provided some of the greatest interest in the site with numerous pre-processing components along with the quaint control room.
The only component of the kiln that was really accessible consisted of the cooler section. The layout here, as mentioned somewhere above, is a planetary system and with enough photoshoppery it would easily make a good set for some sort of star wars mega death cannon.
It wasn't really possible to progress any further, due to the integrity of the building, yet there was enough from here to admire.
The control room was relatively unassuming from the outside as it presented itself as a pre-fabricated box with a lot of the piping for the kilns firing tube splitting the building in half.
The inside was certainly a surprise with the diffused lighting and green panelling making it an appealing interior. The panel was surprisingly easy to decipher with the whole kiln, motor, precipitators, clinker conveyors, and the connecting components attached across the boards' length.
Behind the control room and kiln stood a maze of pipe work and machinery for suppling the kilns with power, heat and processing of the clinker product.
TO BE CONTINUED
Last edited: